Turn ideas into reality
START has rich experience in roll forming machine manufacturing and processing technology. Our geographical location and surrounding supporting industries can meet all metal and mechanical structure manufacturing, as well as supporting customization for specific needs of customers. We provide fully automated turnkey solutions for roll forming lines that integrate feeding, roll forming, cutting, inspection running and stacker packaging handling systems, managed by our custom developed control systems.
We are responsible for the project installation and commissioning of equipment in any country, and once the system is in operation, we provide our own equipment and process monitoring infrastructure for diagnostics in the event of errors, preventive maintenance of equipment, and machine operation and machining processes Continuous optimization of conditions.
Flexible manufacturing
Reliable manufacturing technology can meet the needs of customers’ customized products. Diversified and flexible processing equipment, the ultimate goal is to guarantee efficient and flexible production in a short time.According to the profile or sheet that the customer needs to produce, we will evaluate which structure of the machine is more suitable, for example, is the front punching more suitable, or the post punching more suitable, the front cutting is more suitable, or the post cutting is more suitable? According to the thickness of the coil, the evaluation is which capacity decoiler is suitable, whether to use manual decoiler or hydraulical decoiler? According to the customer’s requirements for speed, decide whether the transmission mode of the machine is chain drive, gear drive, or gear box drive? According to the arrangement and size of the hole pattern of metal products, it is judged whether the punching is online hydraulic punching, or punching first and then forming, etc. We will flexibly configure the parameters of the equipment according to the special products and the customer’s positioning needs of the equipment.
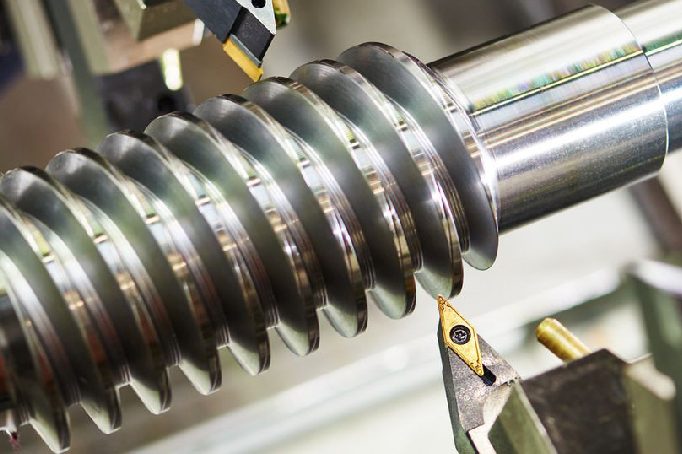
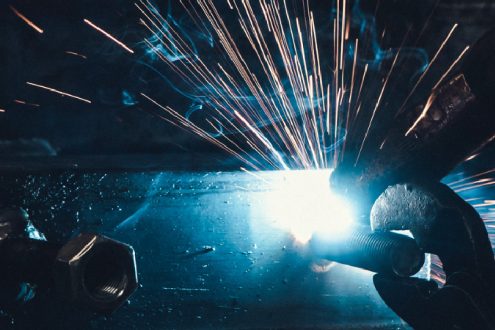
Reliable welding technology
We use reliable arc welding technology, which has a wide range of applications and is commonly used in all metal structures such as automobiles, railway vehicles, ships, aircraft, buildings and construction machinery. The base material is usually steel, but other metals such as aluminium and titanium are also used, and this arc welding guarantees a strong and durable machine weld!
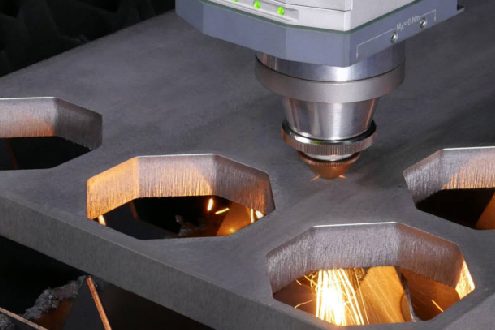
Short and quick delivery time
We will strictly and carefully check the drawings of the metal profiles products with the customer and after the confirmation of the customer, we will carry out the production in an orderly manner. First, we will design the overall drawings of the machine, the drawings of each forming roller, and the machine. The design of each component roller, etc., and then put into production, followed by assembly, test operation, etc., this series of production processes will be arranged in an orderly manner, with the fastest time, about 30-45 working days, delivery. Satisfied equipment for customers!
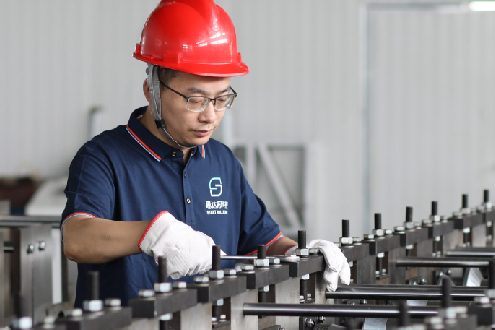
Strict Assembly
Strict assembly after each part of the machine is processed and the quality supervision department measures and inspects each drawing, it will be assembled next. When assembling the machine, make sure to use regular tools and standardized procedures to assemble the machine. After professional training, our workers have mature operating skills and carefully and carefully assemble our equipment
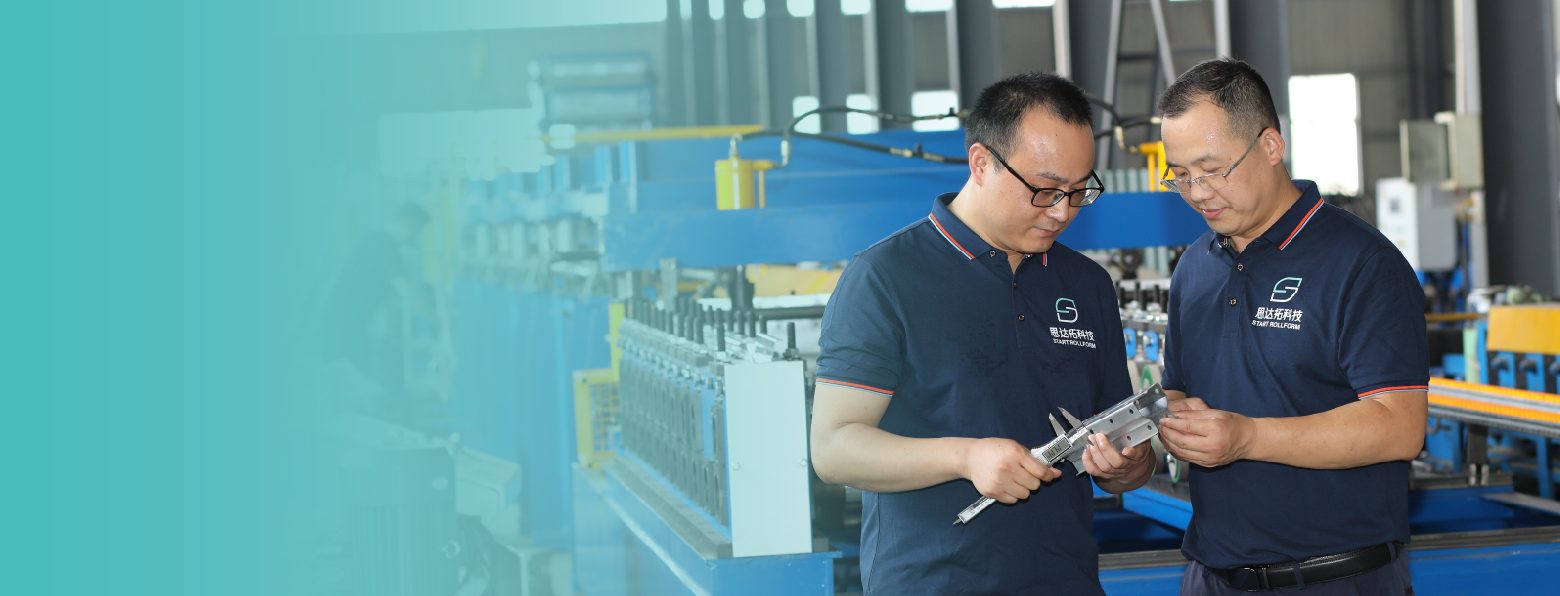
Reliable Quality
We establish a comprehensive and strict quality management system, implement the 6 SIGMA quality plan, support customer service, design, quality, cost control and full on-time delivery, and continuously improve all business processes to lay the foundation for high-quality products.
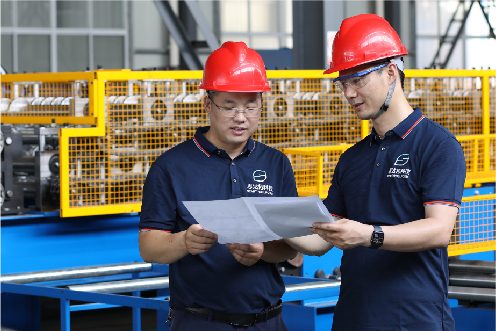
Process quality control
Each department of the factory strictly controls the process of each production according to the ISO9001 quality system. We have advanced drawing software and high-performance machining equipments.
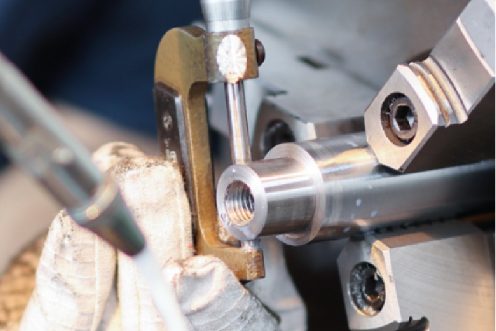
Machining Accuracy Check
For the inspection of the machining accuracy of the parts, we carry out strict inspections from different aspects, mainly from the following aspects: the inspection of the geometric accuracy of the parts, the inspection of the surface quality, the inspection of the mechanical properties and the inspection of hidden defects.
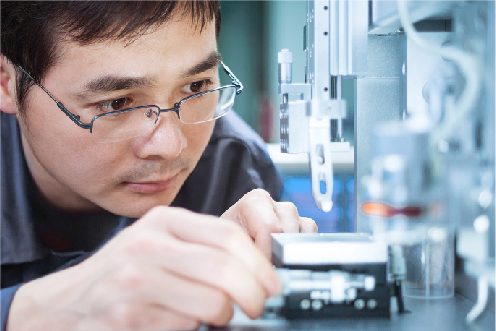
Running Testing
Running testing for the running test of the roll formingmachine, it is mainly to measure the metal finished product produced by the machine according to the confirmed drawing of the metal finished product, whether it strictly matches the drawing. After repeated machine operation tests, we will adjust the rollers, bearings, and cutters according to the operation of the equipment to achieve the best state of the machine.